Montana's Natural Fiber
Young people saw its value first, says Diana Blair of Kalispell’s Going to the Sun Fiber Mill. “Hey, look at the dreads,” they said, reaching for the llama fiber that hung like ropes from her vendor booth. “I’m going to use this to drape my purse.”
“I’m going to make a scarf. Won’t it be wonderfully warm? It’s so soft,” said another.
The next year, her Mammoth Dreads yarn sold out. So did her handmade Avalanche Hats and other products spun from the fleece of llamas and alpacas, fiber once worn only by royalty and considered by Americans as exotic. Today, camelids are as integral to Montana’s natural fiber industry as sheep and goats and hardworking people.
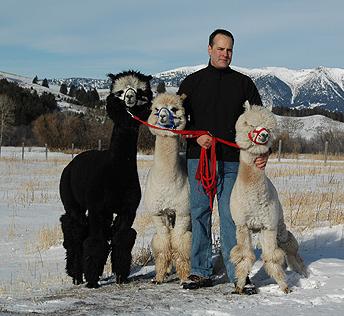
“The thing that people started learning,” says Ed James, owner of the Sugarloaf Wool Carding Mill near Phillipsburg, “natural fiber — it doesn’t matter what it is — it’s the healthiest fiber you can use in clothing and bedding.”
In explanation, Ed starts talking about air pockets and tight crimp and the fiber’s ability to wick away moisture and regulate body temperature.
“What wool does,“ he says, “it takes your own body temperature and radiates it back. Your heart doesn’t have to warm you up, or cool you down. So you have an even heartbeat all night long.”
The Sugarloaf’s best-selling items are pillows. “The wife made herself a wool pillow and slept so restful. Then I tried one, too.“
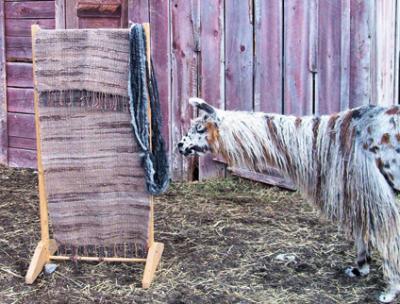
Today, Sue and Ed sell three sizes, and a travel line, that offers all the benefits of natural fiber: It’s durable and longlasting, fire-resistant, and re-useable. Though wool is not completely hypo-allergenic (as is fiber from camelids, their breeders point out), Ed notes that wool prevents dust mites and bacteria growth and that most people are reacting to “the harsh, toxic chemicals that go into conventional” products, rather than the lanolin in wool.
In Montana, most of the natural fiber industry uses a more skin- and eco-friendly approach. Thirteen Mile Lamb and Wool Company uses chemical-free grass, no antibiotics or synthetic hormones, and a citrus-based wash. Many ranches are also predator-friendly, using guard dogs and llamas to protect their herds.
“Llamas are formidable protectors,” says Diana, who cares for 23 llamas and several alpacas. It’s she who provides perhaps the Number One Answer for investing in Montana natural fiber: It’s something beautifully unique, an heirloom well worth its price.
“I’ve still got the first pair of alpaca socks I ever bought,” she says. “I paid $10. Today, they‘d cost $28.”
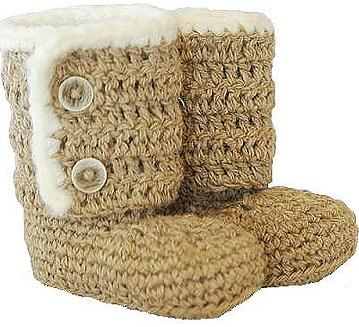
President of the Yellowstone Alpaca Breeders Association — and owner of Northern Rocky Mountain Alpacas, which has the more world-rare suri alpaca (think long, lustrous, human-like hair) — Dennis L. Duenas says, “Most of the good fiber from South America goes to Korea, Italy, or China, where it’s used in high-end fashion. Here, it’s still a cottage industry.”
Erv Lischke of Rocking L Alpacas admits his best-selling items are imported. He says 99% of the camelid garments sold in this country come from Peru, Bolivia, or Chile: countries with millions of animals, commercial mills, and low-wage workers. Here, in the US, there are about 350,00 alpacas and llamas; big mills are geared for wool; and hand knitters are hard to find.
“This makes Montana a quality boutique market,” says James Budd, owner of Alpacas of Montana with his wife, Sarah. Recently successful in their quest to wash and dry their fiber without shrinkage (a world feat that has them in high-level talks), they sell online and collaborate with upscale retail stores. Annually, they use about 2,000 pounds of fiber, create a line of socks and long underwear developed for the industrial commercial market, and they employ some 30 Montanans to knit individually unique alpaca hats, gloves, scarves, rugs, and baby products.
“We use three different mills and the old-school hand-spinners to make the yarn,” explains Sarah, “and then we send it out to knitters throughout the state and encourage them to knit as fast as they can.”
A passionate industry advocate, Diana is one of those knitters. She’s also a certified judge of most fiber, including cashmere and mohair. She says “The best mohair I’ve ever seen is” at Wolverton Mountain Montana.
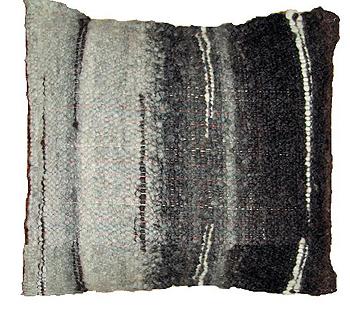
Pleased by the compliment, Debra Wolverton explains that she and her husband, Laramie, raise angora goats and process their fiber near Arlee, and that mohair is nicknamed The Diamond Fiber because of its luster.
She says, “It takes dye beautifully. No two skeins of handspun yarn are ever alike. That’s the mark of true value for those wanting something totally unique, or those wanting to get their hands on this fiber to build something of their own.”
Becky Weed of Thirteen Mile Lamb and Wool has been raising sheep with her husband, Dave, for 25 years near Belgrade. They got into the business because they wanted to spin yarn in Montana. Today, they “spend a lot of time processing for other growers.”
Whether sheep, alpaca or bison, Becky says, “I really like the idea of making it possible for other growers to add value to their fiber. It’s a lot of work, and we’re not going to get rich doing this, but I’m fascinated by all the diversity that grows on grass.”
So is Rickie van Berkum of Raven Ridge Fiber Arts near Missoula. Like Diana (who is known for her blend of bamboo and alpaca), or Debra (who mixes mohair with wool and camelid fiber), Rickie is an inventor, but her specialty is color combinations inspired by the Montana landscape.
“I work with shepherds,” she says, “to dye wool for hand-spinners and yarn for knitters. It’s exciting to be part of the process.”
Erv says, “It’s not just women and knitters who want to touch and feel the [alpaca] fiber. It’s men. Guys will come in and squeeze skeins of yarn” at the farmer’s markets and fairs that he and his wife, Maureen, attend.
“Spinning is a young kid and an old-guy magnet,” agrees Debra Wolverton. “The old guy is trying to figure out how it works, and kids want to know what you’re doing.”
“We’re very much a networking business,” says James, speaking of camelids, but also about Montana‘s fiber industry, including the sheep ranchers, who are experiencing something of a rebound. “We have to grow together, business to business, farm to farm.”
Accordingly, visitors are welcome, particularly during shearing. And fiber producer-artists are eager to meet those who might get into the business some day.
Says Debra, remembering a recent after-school program, “There’s nothing better than when a six-year-old tells you he’s just gotten the best gift ever” by learning to spin fiber.
“When they get their hands on it,” she says, “that’s when you got ‘em.”
~ Glenda Wallace is a western Montana writer who loves warm, beautiful, soft things, which is why she feeds her cat and will wander through fiber-fabric venues with her generous gift-giving, knitter-friend Melee.
Leave a Comment Here